Hibbing, Minnesota – When you enter a career in manufacturing, you not only build a life for yourself, but you also (quite literally) build the world around you. It’s a rock-solid, rewarding career path, one for which many career-seeking young people would be a great fit.
While the manufacturing industry is looking for its next generation of craftspeople to build the products and materials that make modern life run (including the industry-renowned Mesabi radiator), many young people are being pushed in a different direction. Educators, parents, and counselors alike often encourage young people to obtain a four-year college degree instead of entering the work force or learning a trade. This is also a great path, unless you are a student who thrives on working with your hands, solving problems, and seeing the outcome of your work change lives.
That’s why Eric Rewertz, Production Manager at L&M Radiator’s Hibbing location, works tirelessly to open doors for young people to explore all options available to them before diving headfirst into adulthood. As a result of this work and the work of many other educators and industry professionals across the nation, there has been a recent increase of students seeking manufacturing programs instead of the traditional post-secondary path.
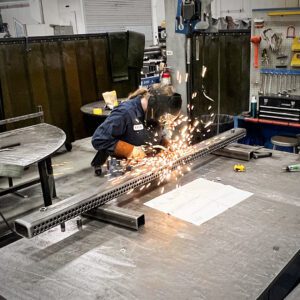
“It’s important to introduce students to the manufacturing world because a lot of the time, as a young adult, you don’t know what you want to do coming out of high school. Work-based learning initiatives give kids the opportunity to spend some time in the industry and to see what our company and others have to offer. They’re able to learn whether or not manufacturing is for them, so exposing them to it while they’re in high school allows them to explore what they want,” said Rewertz. “From our standpoint, it’s a win-win for us and for the students. We get to see a lot of different faces come through and we capture the interest of some good ones.”
Investing in incoming young professionals is essential for the future of manufacturing. L&M Radiator offers multiple work-based learning initiatives that encourage students to dive deeper into their interests in manufacturing while providing expert instruction and support. L&M Welding Supervisors Steve Tanski and Derek Fink are other champions of the career-focused learning opportunities at L&M Radiator. Tanski and Fink work directly with students to guide them through the learning process in a way that caters to each individual student’s strengths and pace.
Collaborating with Local Schools on Career Readiness
L&M typically opens its doors to people who haven’t been given proper introduction to the working world — partnering with local high schools and programs to familiarize students with a real-world manufacturing setting. This collaboration not only educates students about the industry but also provides them with valuable hands-on experience, bridging the gap between academic learning and practical application.
Each visit starts with a tour of L&M’s manufacturing facility in Hibbing, including a brief history on L&M Radiator, which exposes students to the inner-workings of a day-to-day life at one of the most successful manufacturing companies in the world. Some days there might be 15 or so students from one school, and on other days there may be three separate schools that tour the company’s plant.
“Students are not able to work in the shop until they’re 18-years-old. So, many will come through for a tour, observe our workers, see how things are organized, how our weld shop is set up, how we approach cleanliness and quality, and more. It gives them a good introduction to what manufacturing is all about because we have a lot of different departments that they get to see along the way,” said Rewertz.
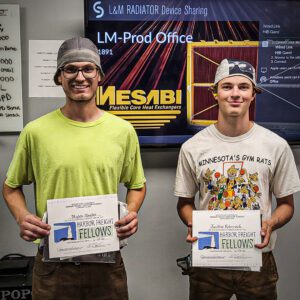
One such partnership is with the Itasca Area Schools Collaborative (IASC) where students come in daily for a few hours to work on projects and also receive payment for their time. These hours are flexible as L&M remains committed to accommodating the schedules of the students who balance school responsibilities with extracurricular activities such as sports, which ensures that students can prioritize their education while also gaining work experience. The program is three months long, usually running from March until the end of May when the regular school year finishes. Some students who discover they have an affinity for the work stay at L&M throughout the summer and work full-time.
During this learning experience, students collaborate with various departments to design and create their very own product. They receive guidance from mentors throughout the entire process, from drafting and prepping to building and painting their final product.
“The students grow in confidence knowing they can see a project through from start to finish,” said Fink. “It’s a big job working here, to come in and start welding with little to no experience. They’re a little shy at first, but they can pick it up pretty quick and go on their own.”
“I’ve been interested in manufacturing my whole life,” said Tanski. “I have more than 40 years of experience, so I understand the benefits that come with a career in manufacturing, and I take those benefits and implement them into these programs. It’s all about practice. We work with the students for as long as we can. We work and work and work until they’re successful.”
The Impact of Mentorship in Manufacturing Careers
Gaining hands-on experience is even more beneficial when you have a supportive mentor guiding you through the process. A key factor to the success of career-focused programs are the mentors who recall their own beginnings in manufacturing jobs. They bring valuable insight as professionals who once started at ground zero then advanced into a higher level of production expertise.
“The whole program reflects that of onboarding with a new employee. The students are treated as if they’re getting hired on full-time. We assign each student a mentor – someone to whom they can turn and ask questions. They’re the go-to person, and you’ll be with that mentor until you feel comfortable on your own,” said Rewertz. “L&M takes a lot of pride in how we introduce new employees to our facility. When you come through our doors, our goal is to have you succeed. You will always have someone to rely on and help you get to where you need to be.”
Mentoring young professionals is as rewarding for L&M employees as their jobs themselves. From start to finish, mentors want to see students succeed, celebrating achievements in various forms. It’s a mutually beneficial relationship that enhances the overall dynamics of the workplace and contributes to a vibrant learning culture.
“We’re working with a student that has recently felt pretty happy about her welding abilities,” said Fink. “She gets really excited to work on stuff because for a while she was just shadowing and practicing welding. Now, we’ve practiced enough where her welds are good enough for her to start working on products alone. It’s really fun to watch her enjoy doing the work.”
At L&M Radiator, there is a wealth of highly qualified mentors available. Alongside Fink and Tanski, Clayton Brown, Tom Simonson, Felicia Jarva, Hunter Maki, Alex Castaneri and others have been instrumental in shaping the careers of young professionals who pass through the facility doors. Community partners such as Joe Gabardi, Welding Instructor at Nashwauk-Keewatin High School have also played an essential role in mentoring and checking in with students and their progress. Their dedicated mentoring ensures that every trainee not only learns the ropes but also embraces the confidence to excel in their respective manufacturing roles.
“Manufacturing is a great career path for young people to join, not only because it will allow them to have a rewarding career, but because we need them. The older generation is going away, so we need to get young people interested in building the future world,” said Tanski.
L&M Radiator’s commitment to mentoring and training the next generation of manufacturing professionals is not only shaping the future of the industry but also enriching the community. Through partnerships with local schools and the implementation of hands-on, work-based learning initiatives, L&M provides invaluable real-world experience to young students. This approach encourages students to not only gain skills but also understand the dynamics of a professional manufacturing setting. By fostering a supportive environment with skilled mentors, L&M Radiator enhances career readiness and personal development for aspiring young workers.
Educators, Parents, and Counselors: Get Involved
Are you interested in applying for a work-based learning initiative? Are you an educator who wants to give their students exposure to great career possibilities in manufacturing? Visit mesabi.com and apply online today. For more information, contact Eric Rewertz at eric.rewertz@wabtec.com.
For more information about Mesabi products, visit Products or www.Mesabi.com
For more stories similar to this one, visit The Mesabi Exchange.